Opening the Power of Welding WPS: Methods for Efficiency and Safety in Manufacture
In the realm of fabrication, Welding Treatment Specifications (WPS) stand as the foundation of welding procedures, dictating the essential steps for achieving both performance and safety in the manufacture procedure. Understanding the intricacies of WPS is extremely important to utilizing its full capacity, yet many companies struggle to open the real power that lies within these records (welding WPS). By delving right into the techniques that maximize welding WPS, a world of boosted efficiency and enhanced safety and security waits for those going to explore the nuances of this important facet of manufacture

Relevance of Welding WPS
The value of Welding Procedure Specifications (WPS) in the manufacture market can not be overstated. WPS work as a crucial roadmap that describes the necessary actions to guarantee welds are performed continually and properly. By defining crucial specifications such as welding processes, products, joint styles, preheat temperature levels, interpass temperature levels, filler metals, and post-weld heat treatment demands, WPS give a standard technique to welding that boosts performance, top quality, and safety in fabrication processes.
Adherence to WPS assists in attaining harmony in weld top quality, decreasing the possibility of flaws or architectural failings. This standardization additionally promotes compliance with industry regulations and codes, making certain that produced frameworks meet the required security requirements. Furthermore, WPS documentation allows welders to duplicate successful welding procedures, bring about regular outcomes across various projects.
Basically, the careful development and rigorous adherence to Welding Treatment Requirements are extremely important for promoting the honesty of bonded structures, safeguarding versus prospective risks, and upholding the reputation of fabrication companies for providing high-grade products and services.
Crucial Element of Welding WPS
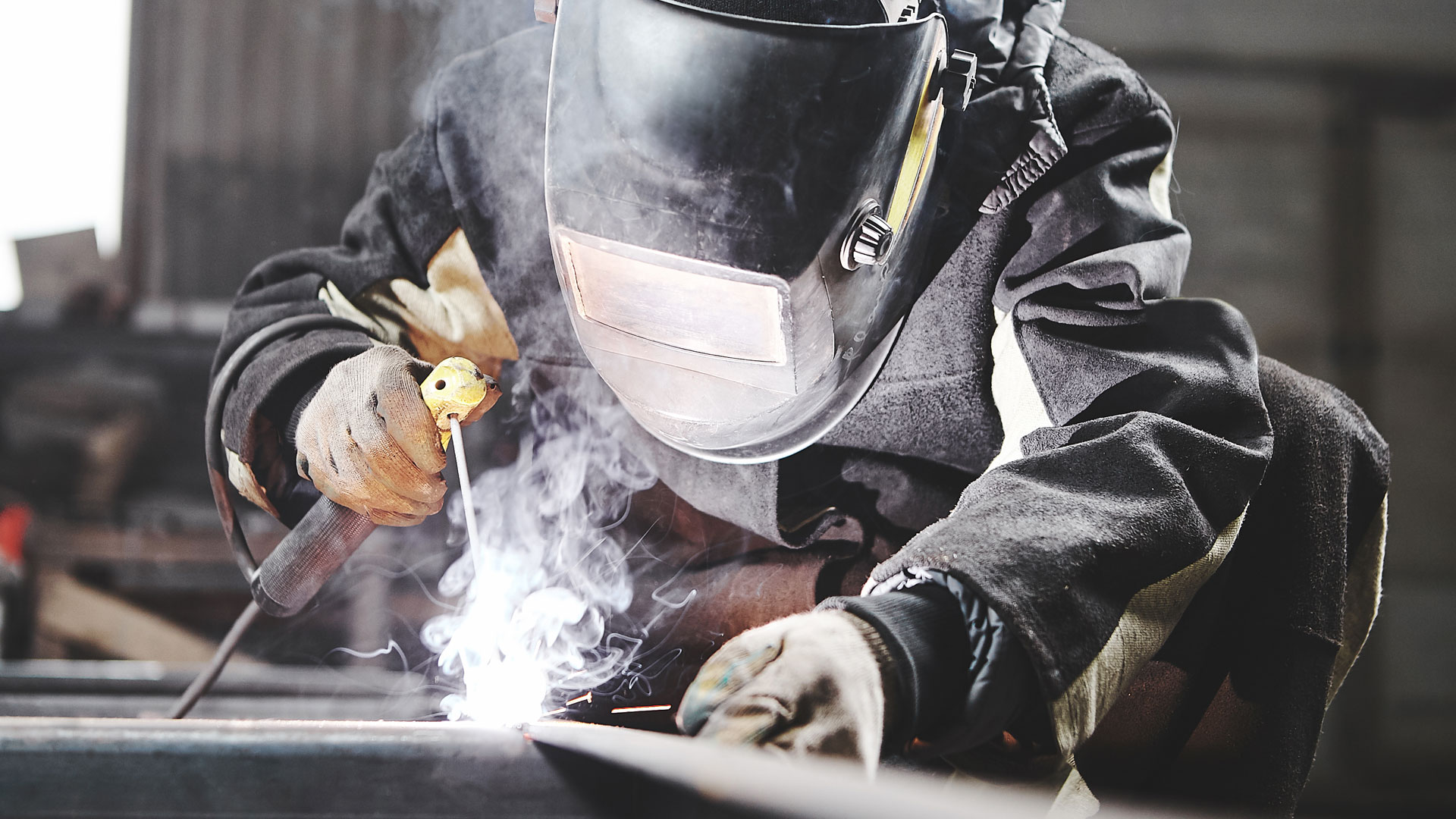
Enhancing Efficiency With WPS
When maximizing welding operations, leveraging the crucial aspects detailed in Welding Procedure Requirements (WPS) comes to be important for maximizing and simplifying processes efficiency. One method to improve effectiveness with WPS is by carefully picking the proper welding specifications.
Frequently assessing and updating the WPS to incorporate any kind of lessons discovered or technological innovations can also add to performance enhancements in welding procedures. By embracing the guidelines established forth in the WPS and continuously looking for ways to maximize processes, fabricators can attain greater performance degrees and remarkable end results.
Ensuring Safety And Security in Construction
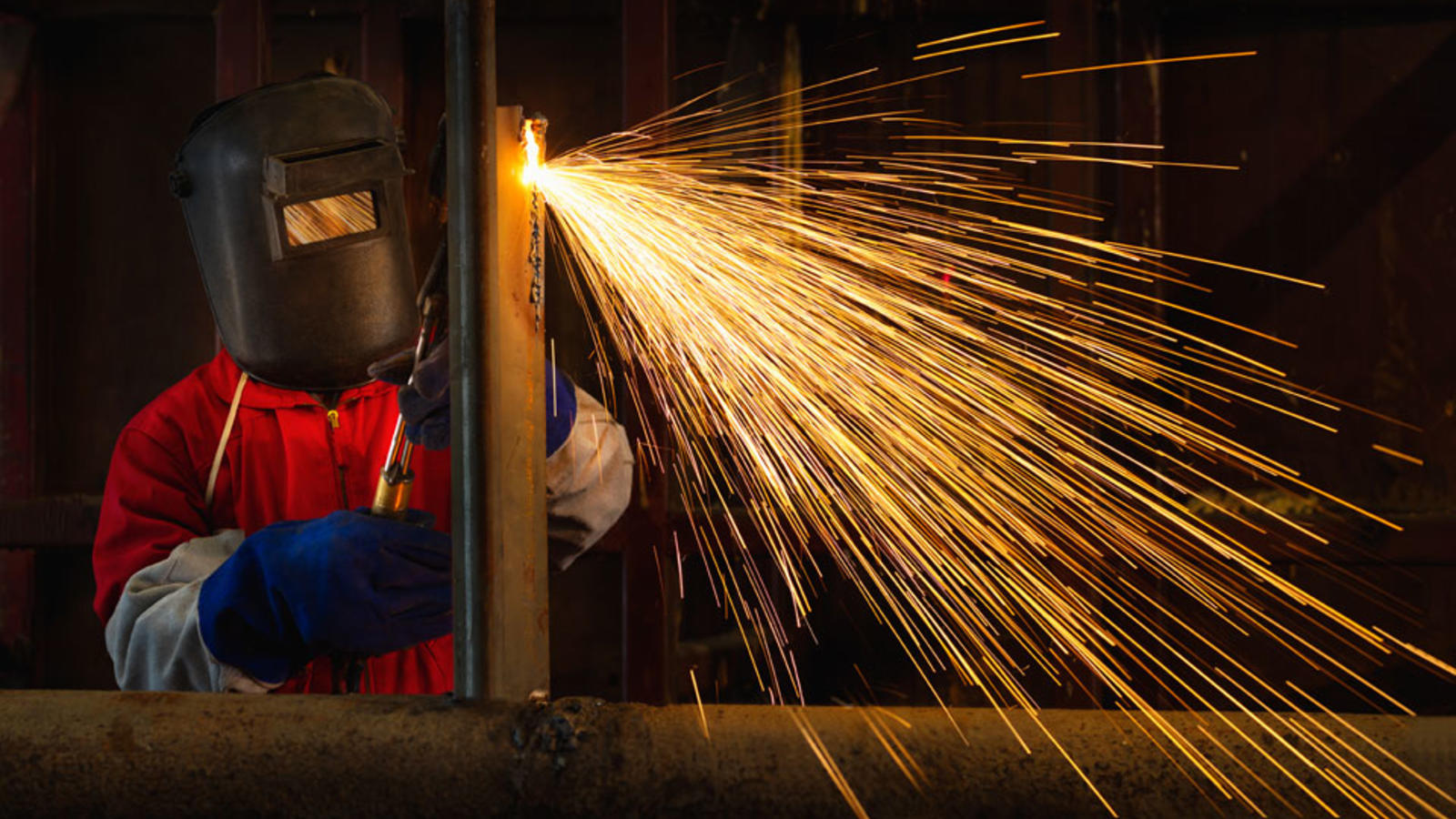
Safety procedures in construction play a crucial function in protecting personnel and maximizing functional treatments. Ensuring safety in fabrication involves a multifaceted strategy that incorporates different aspects of the welding process. One basic element is the provision of individual safety tools (PPE) customized to the particular hazards existing in the fabrication setting. Welders have to be equipped with proper gear such as safety helmets, gloves, and protective apparel to click resources minimize dangers related to welding activities.
Furthermore, adherence to proper ventilation and fume removal systems is vital in preserving a healthy work setting. Welding fumes contain dangerous materials that, if inhaled, can posture serious wellness dangers. Executing efficient ventilation steps assists to lessen direct exposure to these unsafe fumes, advertising respiratory system health amongst employees.
Normal devices upkeep and inspections are also essential for making certain safety and security in construction. Damaged equipment can bring about crashes and injuries, emphasizing the value of prompt repair services and routine checks. By focusing on precaution and cultivating a society of understanding, manufacture facilities can develop a effective and safe workplace for their workers.
Implementing WPS Finest Practices
To improve functional performance and guarantee high quality end results in fabrication procedures, incorporating Welding Treatment Spec (WPS) ideal methods is critical - welding WPS. Applying WPS finest practices entails careful planning, adherence to industry requirements, and continuous tracking to assure optimum results. Firstly, selecting the appropriate welding procedure, filler product, and preheat temperature level defined in the WPS is vital for accomplishing the preferred weld high quality. Secondly, ensuring that qualified welders with the essential qualifications perform the welding treatments according to the WPS guidelines is important for uniformity and integrity. Consistently updating and reviewing WPS papers to reflect any kind of procedure enhancements or modifications in materials is also an essential finest technique to maintain precision and significance. Additionally, offering thorough training to welding employees on WPS demands and ideal practices cultivates a culture of safety and security and high quality within the fabrication environment. By vigilantly applying WPS finest techniques, fabricators can improve their procedures, decrease errors, and deliver exceptional products to meet client assumptions.
Conclusion
In conclusion, welding WPS plays an essential role in making certain performance and security in fabrication procedures. By adhering to these techniques, companies can unlock the full potential of welding WPS in their fabrication operations.
In the realm of construction, Welding Treatment Specs (WPS) why not look here stand as the foundation of welding operations, dictating the required steps for achieving both performance and safety in the construction procedure. By specifying vital specifications such as welding processes, products, joint layouts, preheat temperature levels, interpass temperature levels, filler steels, and post-weld warmth treatment needs, WPS give a standard technique to welding that improves efficiency, quality, and safety and security in manufacture processes.

When maximizing welding operations, leveraging the crucial components described in Welding Treatment Requirements (WPS) becomes necessary for taking full advantage of and simplifying processes productivity. (welding WPS)
Comments on “Producing a Welding WPS: Step-by-Step Recommendations for Professionals”